Modulaire Group (Modulaire) is Europe and Asia Pacific’s leading specialist in modular services and infrastructure. Combining unrivalled skill and adaptability, we create smart spaces for people to work, learn and live. We deliver added value for our customers through our equipment, connectivity and furniture solutions. With operations in 23 countries, and over 330,000 modular units, our skilled workforce delivers the space solutions our customers need.
This is our fifth annual Environment, Social, Governance and Sustainability (ESGS) report, which shares our impacts, priorities, actions, and progress from 1 January 2024 to 31 December 2024 (unless otherwise stated). The focus areas are informed by our double materiality process, meeting the needs of our business strategy. All of our operations are in scope unless otherwise stated. We commit to sharing this information with our stakeholders through our communication channels. We integrate the TCFD (Task Force on Climate-related Financial Disclosures) four pillar framework into our reporting structure, believing in its principles of effective disclosure, with sections on Governance, Strategy, Risk Management, and Metrics and Targets. By using these principles and the latest reporting developments, Modulaire will ensure our practices remain aligned with best practice sustainability standards.
Modulaire ESGS Report 2024
Building our future
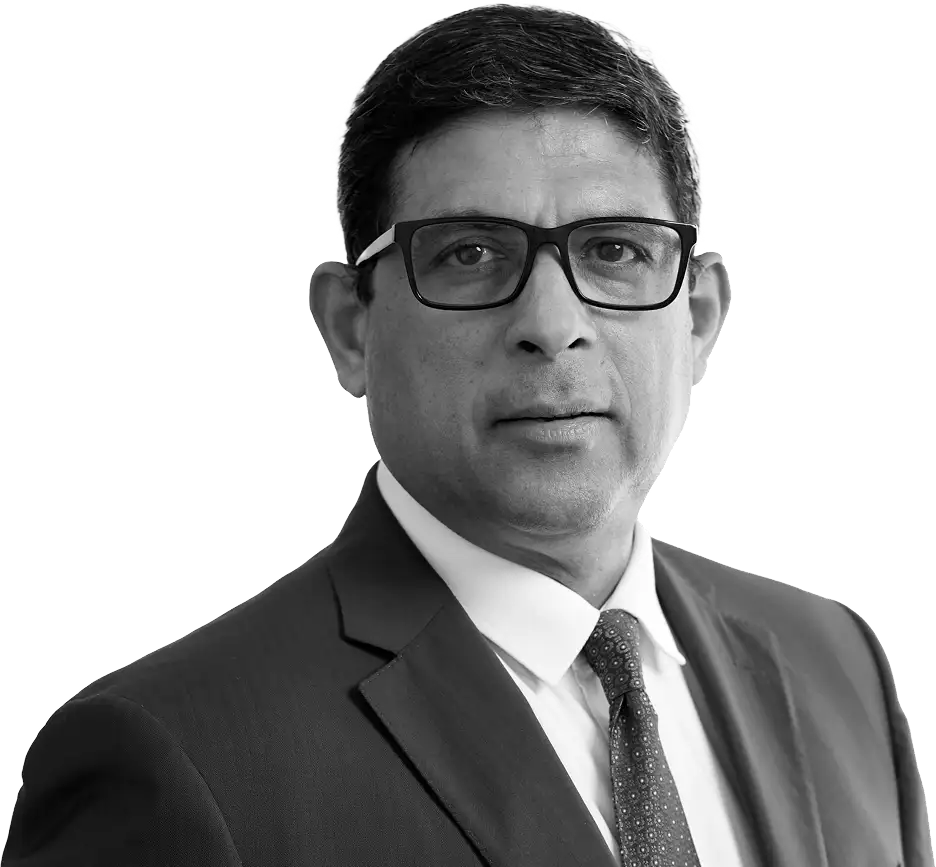
“We are redefining the future of the built environment with a steadfast dedication to sustainability, circular economy principles, technological advancements, and modular design. Every space we create embodies resilience, efficiency, and connectivity - serving businesses and communities while safeguarding the environment.”
Pavan Pattada, Group Chief Executive Officer
Our approach is driven by the transformative forces of evolving megatrends, national ESG targets, sector dynamics, societal shifts, customer requirements, and industry advancements. By strategically aligning with these critical factors, we maximise our ability to create long-term value across every stage. Our unwavering commitment to excellence ensures the delivery of safe, high-quality, and fully compliant spaces and products - providing our customers with tailored solutions that meet their unique needs and expectations.
By embracing a circular economy approach, we prioritise refurbishment and material reuse, minimising waste and ensuring resources remain in continuous circulation. The emergence of smart cities, powered by AI and Internet of Things, is revolutionising urban living - making it smarter, more efficient, and seamlessly interconnected.
In my first year as CEO, I have deeply valued meeting with our people, customers, suppliers, and investors. The potential for our modular solutions is vast, and we are committed to expanding our successes across all markets.
With the growing demand for sustainable goods and services, we remain focused on innovation - developing value-added products and services that contribute to a low-carbon future.
This year, our decarbonisation efforts have yielded a 41% reduction in Scope 1 and 2 absolute emissions since 2020. Prioritising electrification, 22% of our cars and 35% of our forklifts have transitioned to electric. Our newest service centre in Karlstein, Germany, is at the cutting edge of sustainable design and will enable us to share learnings and best practice from the site across the Group.
Our mission is clear: to shape the future with purpose, sustainability, and innovation at its core - meeting the evolving needs of our stakeholders. The circular economy is not just our strategy; it is the foundation upon which we build the future.
Key megatrends shaping the built environment
Performance highlights 2024
Environmental
- 87%less Waste
to landfill since 2020
per typical unit - Net Zerotargetssubmitted to SBTi
- 41%less GHG emissionsScope 1 & 2 absolute market-based since 2020
- 64%less Watersince 2020 per typical unit
- 78%Renewable energy
Social
- 30%lower LTAFRsince 2023
- 5,442hourspaid volunteering
- 3%more female employeesoverall proportion since 2020
- 3UN daysParticipated in International Women’s Day; World Day for Safety & Health at Work; and World Environment Day
Governance
- 2,070hoursCode of Ethics training, including Anti-bribery and Corruption
- 11EcoVadis medals6 Gold medals
5 Silver medals - 117hoursCybersecurity training
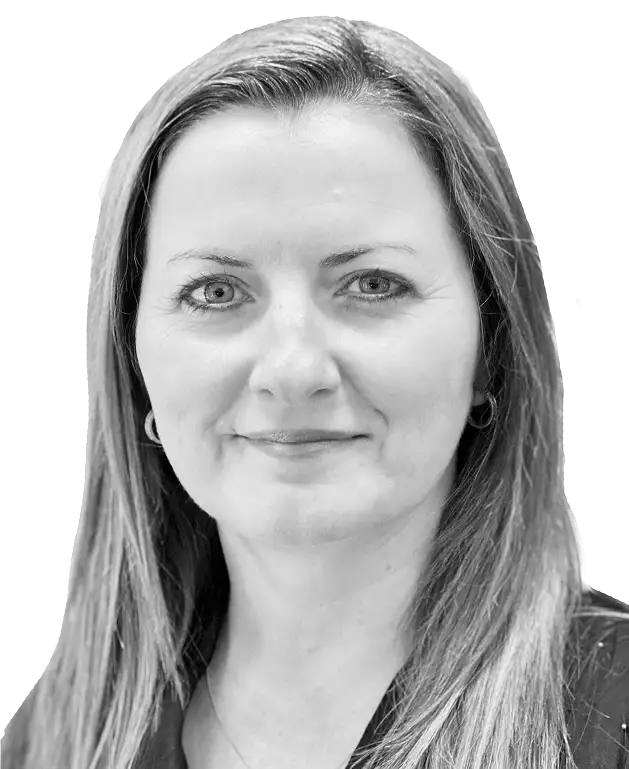
“The relationship between Finance and ESGS is pivotal. By integrating ESGS considerations into financial decision-making, we drive sustainable growth and manage oversight of our impacts and risks and we can act on opportunities for value creation. This fosters a more resilient and a robust approach. In 2024, ahead of regulatory change, the Board has assigned responsibility for ESG compliance to the Audit & Risk Committee and appointed an ESGS Controller to align internal process..”
Emma Mercer, Group Chief Financial Officer
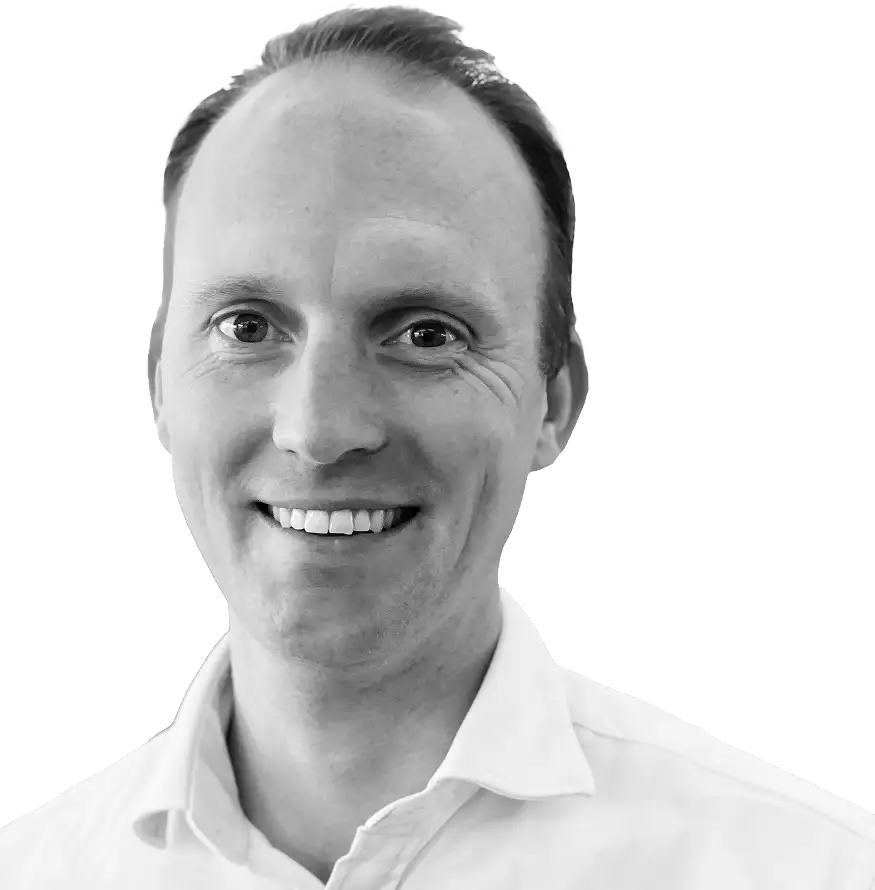
“We have implemented a comprehensive ESGS Responsible Sourcing Policy to embed ethical practices across our supply chain. It is helping us to evaluate and prioritise our impacts and to minimise the risk of human rights violations. The increased transparency it brings benefits everyone and gives emphasis to collaboration, performance evaluation and continuous improvement. We will continue to improve our approach and tools over time. This year, we participated in several ESG audits for key customers that have focused on social impact.”
James Odom, Group General Counsel
Our ESGS purpose
At Modulaire, we create smart spaces for people to work, learn and live. We work with purpose; to help generate economic prosperity, to do social good and promote environmental responsibility. Where we can make a difference, we will with our people and products.
We seek to reduce our environmental impacts and to continuously improve our sustainability performance through responsible governance, processes and practices. Our ESGS purpose is aligned with a number of best practice frameworks and standards, including the UN SDGs, UNGC Principles and the TCFD.
Environmental
- Provide customers with sustainable and circular solutions using our Loops within Loops strategy
- Help to improve the sustainability performance of our supply chain
- Design and deliver safe, energy-efficient, low-carbon solutions to our customers using clean and innovative technology where possible
- Reduce our environmental impacts across energy, carbon,water, waste and biodiversity
Social value
- Provide a safe, inclusive, diverse and motivating environment for our people, contractors and visitors
- Promote organisational change management to meet ESGS commitments
- Empower our employees to add value for our customers, suppliers and communities
- For communities, act responsibly and create social value through our group initiatives and focused local programmes
Governance
- Strict compliance with applicable local legislation relating to ESGS
- All functions and business units contribute and report on Modulaire’s ESGS commitments and targets
- Achieve sustainable growth and robust business performance through responsible corporate governance and an open dialogue with all stakeholders
- Meet sustainability objectives
- Support our commitments to external ESGS frameworks including the UN Sustainable Development Goals, UNGC Principles and the TCFD
Our business strategy
Loops within Loops is our sustainable circular business model. It simply means we use innovative sustainable design solutions to produce modular units that can stay in service longer, going round and round again. This reduces the use of virgin materials, minimising resources and waste. By designing in sustainability and designing out waste, we produce a circular product that can be reused, refurbished, remade and assembled. We do this to meet the expectations of our stakeholder groups, who want maximum value with minimum impact.
Loops within Loops
Our sustainable modular solutions contribute to an advancing circular economy. Whilst we are in the early stages of realising the full potential benefits of our activities, the steps that we are taking to better understand the risks and opportunities of the transition to a low carbon economy are bringing measurable benefits to our customers, the environment and the societies in which we operate.
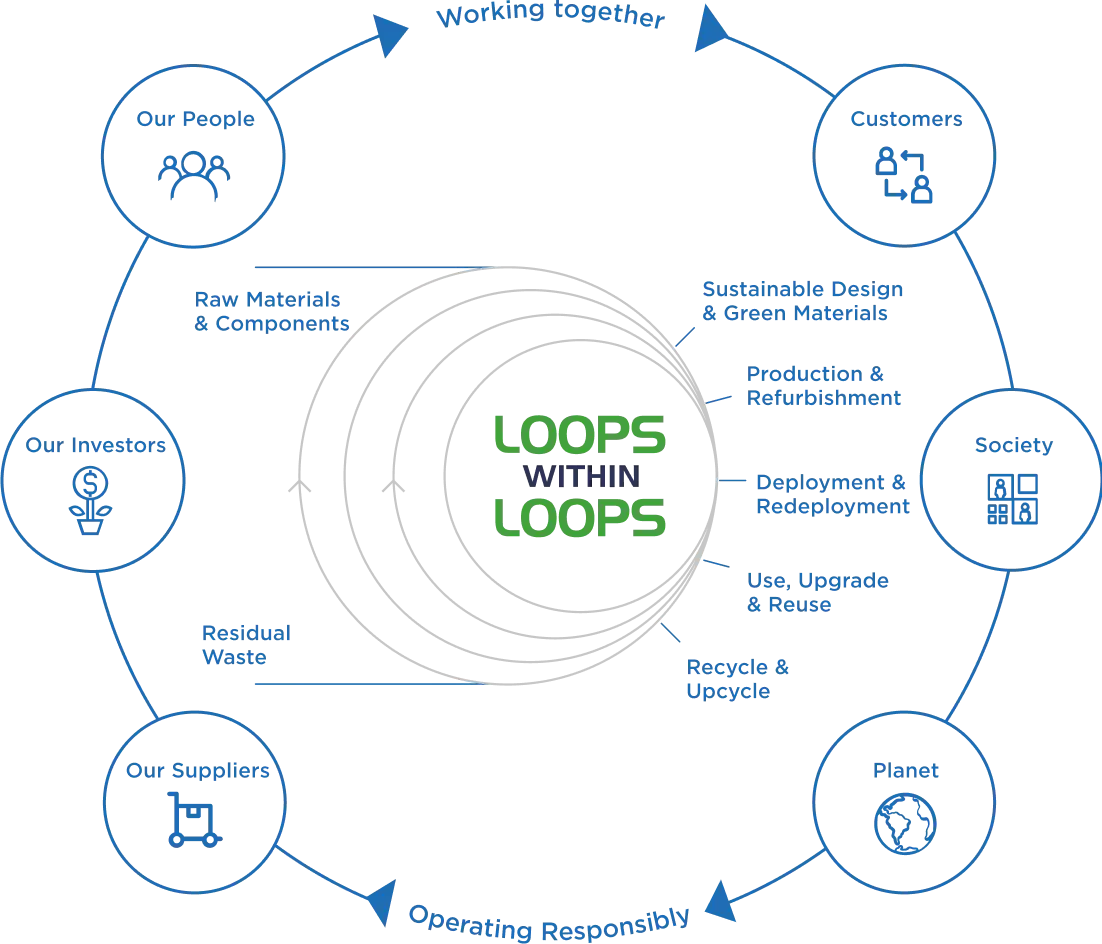